Manufacturers
- Abracon
- Adam Tech
- Aerospace, Defense & Marine
- Agastat
- AIC
- AKM Semiconductor
- Alcoswitch
- Allegro
- Alps Electric
- Altera
- AMI Semiconductor
- AMP
- ams
- Analog Devices (ADI)
- Aptina Imaging
- Atmel
- Avago / Broadcom
- AVX
- Axicom
- Bccomponents
- Beyschlag
- BI Technologies
- Bourns Inc.
- Bowei Integrated Circuits
- Bridgelux
- Buchanan
- California Micro Devices
- Catalyst Semiconductor
- CGS
- Cirrus Logic
- Citizen Electronics
- CML Microcircuits
- Coiltronics
- Cooper Bussmann
- Corcom
- Core Logic
- Cree
- CSR PLC
- CTS
- Cypress Semiconductor
- Dale
- Data Image
- Deutsch
- Diodes Incorporated
- DOMINANT Opto Technologies
- E-T-A
- Eaton
- ECS
- Edison Opto
- Elcon
- EPCOS
- Epistar
- Epson
- Everlight Electronics
- Exar
- Fairchild Semiconductor
- FCI
- Freescale Semiconductor
- Fremont Micro Devices (FMD)
- Fujitsu Semiconductor
- Fulltech Electric
- General Semiconductor
- Harvatek
- Holsworthy
- Hsuan Mao Technology
- IDT
- Infineon Technologies
- Innolux
- International Rectifier (IR)
- Intersil
- IRC
- ISSI
- IXYS-IC
- Jing Cheng Electronical
- JL World
- Johanson Dielectrics
- Johanson Technology
- JRC / NJR
- JST
- KEC
- Kilovac
- Kingbright
- Kyocera Industrial Ceramics
- LEDiL
- Linear Technology / ADI
- Lite-On Technology
- Littelfuse
- Lumex
- Lumileds
- Luminary Micro
- Luminus Devices
- Macronix
- Maojwei / ZJPT
- Maxim Integrated
- MCC
- Mean Well Enterprises
- Microchip Technology
- Micron
- Microsemi
- Mini-Circuits
- Molex
- Murata Manufacturing
- Murata Power Solutions
- MWT
- National Semiconductor
- Nichicon
- Nippon Chemi-Con
- NJR / JRC
- NVE
- NXP Semiconductors
- OEG
- Omnivision
- ON Semiconductor
- Optek Technology
- Optrex
- OSRAM Opto Semiconductors
- OTAX
- Panasonic
- Peregrine(pSemi)
- Potter & Brumfield
- Power Integrations
- PowerStor
- Preci-Dip
- Prewell
- Products Unlimited
- Pulse Electronics
- PulseCore Semiconductor
- Qorvo
- Raychem
- Renesas Electronics
- RFMD
- Richtek Technology
- ROHM Semiconductor
- Rubycon
- Samsung Electro-Mechanics
- Samsung Semiconductor
- Schaffner
- Schrack
- Seiko Instruments, Inc. (SII)
- Semtech
- Sensata
- Seoul Semiconductor
- Sfernice
- Sharp Display
- Sharp Microelectronics
- Silicon Labs
- Siliconix
- Skyworks Solutions
- SoniCrest / JL World
- Spansion
- Sprague
- Stanley Electric
- STMicroelectronics
- Sunny Electronics
- Susumu (SSM)
- Taimag
- Taiyo Yuden
- TDK
- TDK-Lambda
- TE Connectivity
- Teccor
- Texas Instruments (TI)
- Thin Film
- Tianma Micro-electronics
- TOCOS
- TOKO
- Toshiba Electronic Components
- TT Electronics
- Tusonix
- TXC
- Tyntek
- Vishay
- Vishay Precision Group
- Vitramon
- Walsin Technology
- Weidmuller
- Welwyn
- Wickmann
- Winbond
- Xilinx
- Yageo
- Zetex Semiconductors
- ZJPT / Maojwei
News
Panasonic Commercializes an Anti-Glare Type Anti-Reflection Film
2020-10-12 | Return- The film boasts excellent weatherability conforming to the DIN (Deutsche Industrie Norm) Standards and high infrared transmittance
Osaka, Japan – Panasonic Corporation announced today that its Industrial Solutions Company has commercialized an anti-glare type [1] anti-reflection film for automotive displays. A wet process with excellent cost performance was adopted to develop the low reflection film with the model number MUAG8 (G200N). The company has started shipping samples and will start mass production in April 2021.
Progress is being made to upgrade automotive displays, including center information displays and side displays, by addressing the need for larger screens, higher resolution, higher definition, odd form varieties, and improved operability. Under such circumstances, the displays are required to provide high visibility to allow drivers to instantly obtain information for ensuring safe and comfortable driving, creating strong demand for reducing reflection from the displays.
To reduce the reflection from the automotive displays, their outermost surfaces require anti-reflection properties. A method of laminating a film on screens is suited to achieve such anti-reflection. Such method can easily address the need for larger screens and odd form varieties and also prevents screen glass from shattering upon impact. Therefore, a wet process [2] for producing anti-reflection films is adopted to develop the product.
However, there is a problem whereby it is difficult for conventional wet processes to concurrently ensure that produced films have good anti-reflection characteristics and high durability during actual use, while the processes have excellent cost performance advantages, including a short production lead time. Panasonic has achieved the low reflection characteristics of the new film with the reflectance reduced to 0.5% or lower by employing its unique resin design, hard coating material design, and nano-coating technologies.
Moreover, the product has high weatherability that meets the DIN Standards [3] related to deterioration under harsh use environments. In addition, Panasonic's original design technology of optical materials achieves the new film with high infrared transmittance, which is effective when infrared sensors are installed as part of a driver monitoring system incorporated into the periphery of a display. This allows the film to transmit a greater amount of infrared rays. When the film can ensure the amount of infrared rays required for the sensors to detect incoming rays, the film can be attached to the surface of the display with the inside sensors fully covered.
This developed product will be exhibited at the SID Vehicle Displays Online 2020 to be held on October 14 and 15, 2020.
Panasonic's new anti-glare type anti-reflection film for automotive displays has the following features:
1. Achieving low reflection characteristics with a reflectance of 0.5% or lower through a wet process with excellent cost performance for the first time in the industry*
2. Boasting high-level weatherability that conforms to the DIN (Deutsche Industrie Norm) Standards
3. Infrared ray transmittance exceeds 90%
* Panasonic data as of October 12, 2020
Suitable applications:
Automotive displays (including instrument cluster panels), such as center information displays, side displays, and automotive displays equipped with driver monitoring systems on the periphery
[Product Features]
1. Achieving low reflection characteristics with a reflectance of 0.5% or lower through a wet process with excellent cost performance for the first time in the industry
Light incident to an anti-reflection layer reflects on both the front and the back surfaces of the layer. Optimizing the refractive index and thickness of the layer can reverse the phase of the light reflected on the back surface, which can offset all light reflected on the front and the back surfaces to achieve a low reflectivity layer. Panasonic uses its unique resin design and hard coating material design technologies to laminate a combination of multiple high and low refractive-index layers, and further forms them into a film deposited onto a base film by using its unique nano-coating technology. Light reflected from the formed film is reduced by the reflection offset, thereby allowing the company to achieve a low reflectance of 0.5% or lower through a wet process for the first time in the industry.
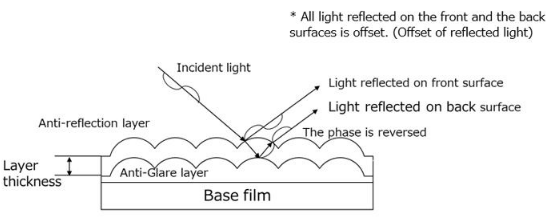
2. Boasting high-level weatherability that conforms to the DIN (Deutsche Industrie Norm) Standards
Under the harsh environments of a car cabin, anti-reflection films are exposed to significant issues related to film deterioration, including discoloration and film peeling. The developed product underwent weatherability testing that conforms to DIN75220 (Z-in 1) [4] that requires repeat exposure of UV irradiation under high temperatures and condensed humidity under low temperatures. After that, the company performed a cross-hatch adhesion test [5] to check the adhesion of the product under harsher conditions and verified that there was no film peeling.
3. Infrared ray transmittance exceeds 90%
Panasonic's original design technology of optical materials achieves the new film with high infrared transmittance, which is effective when infrared sensors are installed as a part of a driver monitoring system incorporated into the periphery of a display. This allows the film to transmit a greater amount of infrared rays. When the film can ensure the amount of infrared rays required for the sensors to detect incoming rays, the film can be attached to the surface of the display with the inside sensors fully covered. This eliminates the need for additional processing such as perforating areas of the film through which sensors receive infrared rays, thereby contributing to the reduction of process steps and the improvement of design quality.
Basic specifications:
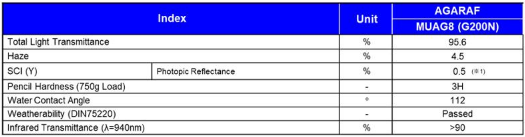
[Description of Terms]
*1 Anti-glare type
Measures for preventing reflection from a film, which has a processed surface with asperities to disperse light from outside, thereby reducing reflection from display surfaces and thus easing the strain on the eyes
*2 Wet process
A method to form coating layers on a base film and subsequently drying and curing the coating layers. This type of process allows quick layer forming and has excellent cost performance because of the short production lead time.
*3 DIN Standards
National standards stipulated by the Deutsche Industrie Norm. These standards are widely referred to internationally, not only in Germany. These are equivalent to the JIS Standards in Japan.
*4 DIN75220 (Z-in 1)
One of the weatherability test conditions specified by the DIN Standards. Refers to environment acceleration tests whereby a sample is exposed to UV irradiation under a high temperature (80°C ) for 15 days and subsequently undergoes repeated cycles of being exposed to condensed humidity under a low temperature (-10°C) and UV irradiation under high temperatures for 10 days.
*5 Cross-hatch adhesion test
This test method comprises the following steps.
Use a box cutter to make incisions horizontally and vertically on the surface of a film to create a lattice pattern with 100 squares.
Apply pressure to adhesive tape on the surface of the cut squares and then remove it to evaluate how closely the coating layer adheres to the base film.
Source:http://industrial.panasonic.com/