Manufacturers
- Abracon
- Adam Tech
- Aerospace, Defense & Marine
- Agastat
- AIC
- AKM Semiconductor
- Alcoswitch
- Allegro
- Alps Electric
- Altera
- AMI Semiconductor
- AMP
- ams
- Analog Devices (ADI)
- Aptina Imaging
- Atmel
- Avago / Broadcom
- AVX
- Axicom
- Bccomponents
- Beyschlag
- BI Technologies
- Bourns Inc.
- Bowei Integrated Circuits
- Bridgelux
- Buchanan
- California Micro Devices
- Catalyst Semiconductor
- CGS
- Cirrus Logic
- Citizen Electronics
- CML Microcircuits
- Coiltronics
- Cooper Bussmann
- Corcom
- Core Logic
- Cree
- CSR PLC
- CTS
- Cypress Semiconductor
- Dale
- Data Image
- Deutsch
- Diodes Incorporated
- DOMINANT Opto Technologies
- E-T-A
- Eaton
- ECS
- Edison Opto
- Elcon
- EPCOS
- Epistar
- Epson
- Everlight Electronics
- Exar
- Fairchild Semiconductor
- FCI
- Freescale Semiconductor
- Fremont Micro Devices (FMD)
- Fujitsu Semiconductor
- Fulltech Electric
- General Semiconductor
- Harvatek
- Holsworthy
- Hsuan Mao Technology
- IDT
- Infineon Technologies
- Innolux
- International Rectifier (IR)
- Intersil
- IRC
- ISSI
- IXYS-IC
- Jing Cheng Electronical
- JL World
- Johanson Dielectrics
- Johanson Technology
- JRC / NJR
- JST
- KEC
- Kilovac
- Kingbright
- Kyocera Industrial Ceramics
- LEDiL
- Linear Technology / ADI
- Lite-On Technology
- Littelfuse
- Lumex
- Lumileds
- Luminary Micro
- Luminus Devices
- Macronix
- Maojwei / ZJPT
- Maxim Integrated
- MCC
- Mean Well Enterprises
- Microchip Technology
- Micron
- Microsemi
- Mini-Circuits
- Molex
- Murata Manufacturing
- Murata Power Solutions
- MWT
- National Semiconductor
- Nichicon
- Nippon Chemi-Con
- NJR / JRC
- NVE
- NXP Semiconductors
- OEG
- Omnivision
- ON Semiconductor
- Optek Technology
- Optrex
- OSRAM Opto Semiconductors
- OTAX
- Panasonic
- Peregrine(pSemi)
- Potter & Brumfield
- Power Integrations
- PowerStor
- Preci-Dip
- Prewell
- Products Unlimited
- Pulse Electronics
- PulseCore Semiconductor
- Qorvo
- Raychem
- Renesas Electronics
- RFMD
- Richtek Technology
- ROHM Semiconductor
- Rubycon
- Samsung Electro-Mechanics
- Samsung Semiconductor
- Schaffner
- Schrack
- Seiko Instruments, Inc. (SII)
- Semtech
- Sensata
- Seoul Semiconductor
- Sfernice
- Sharp Display
- Sharp Microelectronics
- Silicon Labs
- Siliconix
- Skyworks Solutions
- SoniCrest / JL World
- Spansion
- Sprague
- Stanley Electric
- STMicroelectronics
- Sunny Electronics
- Susumu (SSM)
- Taimag
- Taiyo Yuden
- TDK
- TDK-Lambda
- TE Connectivity
- Teccor
- Texas Instruments (TI)
- Thin Film
- Tianma Micro-electronics
- TOCOS
- TOKO
- Toshiba Electronic Components
- TT Electronics
- Tusonix
- TXC
- Tyntek
- Vishay
- Vishay Precision Group
- Vitramon
- Walsin Technology
- Weidmuller
- Welwyn
- Wickmann
- Winbond
- Xilinx
- Yageo
- Zetex Semiconductors
- ZJPT / Maojwei
新闻中心
Industry’s Largest Family of Inductive Position Sensors Now Includes Solution for ISO 26262-Compliant EV Motor Control Applications
2022-06-15 | 返回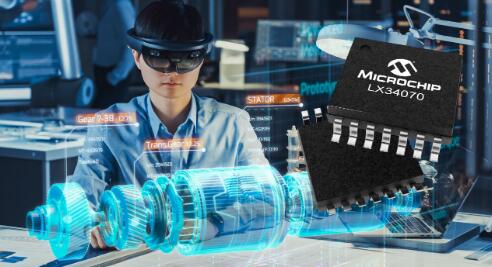
CHANDLER, Ariz., June 15, 2022 — Developers of motor control systems are rapidly replacing Hall Effect position sensors and older magnetic resolver solutions with inductive alternatives that eliminate expensive magnets and other heavy transformer-based structures so they can be integrated onto simple, compact printed circuit boards (PCBs). Extending the world’s broadest line of inductive position sensors into the EV motor control market, Microchip Technology Inc. announces the LX34070 IC that has been purpose-built for EV motor control applications. It includes differential outputs, fast sample rates and features that make it functional-safety-ready for ISO 26262 compliance in the Automotive Safety Integrity Level–C (ASIL–C) classification.
“The LX34070 inductive position sensor enables lighter, smaller, more reliable motor control solutions that meet stringent safety requirements, reduce overall system costs, and can operate seamlessly and precisely in the noisy environment of an automobile’s DC motors, high currents and solenoids,” said Fanie Duvenhage, vice president of Microchip’s mixed signal and linear analog business unit. “Designers can use the LX34070 to further streamline EV motor control designs by pairing it with other functional-safety-ready Microchip devices including our 8-bit AVR® and PIC® microcontrollers, our 32-bit microcontrollers, and our dsPIC® digital signal controllers.”
The LX34070 inductive position sensor solution offers numerous advantages compared to magnetic resolvers and Linear Voltage Differential Transducers (LVDTs), at a fraction of the cost. By using PCB traces rather than transformer-based magnetic windings and coil structures, the LX34070 device has negligible size and mass compared to alternatives that weigh as much as a pound. Accuracy is improved since the LX34070 does not depend on magnet strength, and the device improves robustness by actively rejecting stray magnetic fields. These and other features give designers greater flexibility over where they can place the thin, lightweight PCB-based LX34070 solution in their EV motor control designs.
PCB-based inductive position sensors use a primary coil to generate an AC magnetic field that couples with two secondary coils. A small metal target object disturbs the magnetic field so that each secondary coil receives a different voltage whose ratio is used to calculate absolute position. Using these techniques, Microchip introduced its first high-volume inductive sensor for automotive and industrial applications over a decade ago and has many programs in volume production. The LX34070 now brings the same proven PCB materials, approaches and simplified, low-cost packaging to EV motor control and other applications that need its high-speed and low-latency benefits.
Availability
Microchip’s LX34070 inductive position sensor IC is available today.
Supporting Designers Through ISO 26262 Certification
Microchip works closely with automotive OEMs and suppliers to support their ISO 26262 compliance needs. The company’s functional safety packages give them what they need at various stages of the evaluation and design cycle, including certified safety manuals, Failure Mode Effect and Diagnostics Analysis (FMEDA) reports and, in some cases, diagnostic software such as certified self-test libraries for relevant ASILs. The company also practices customer-driven obsolescence, with Microchip continuing to supply devices as long as there is demand and all components are available, removing the risk of a forced redesign because a part may unexpectedly enter end-of-life (EOL).
Resources
● Application Image: www.flickr.com/photos/microchiptechnology/52115367210/sizes/l
Source: https://www.microchip.com